Following best practices can improve results in aseptic filling lines
Proper Procedures Can Reduce the Risk of Non-Compliance During Autoclaving of Pharmaceutical Closures
Human beings have a natural tendency to push the limits of any system. We overpack our luggage before trips or carry one too many bags home from the grocery store. But sometimes less is more — particularly when it comes to autoclaving components used in an aseptic filling line.
The importance of autoclaving
Autoclaving is critical for contamination prevention, and a proper technique is required for success. The process uses steam heat to kill any microbial life, preventing the introduction of foreign microorganisms into a sterile environment. The steam vapor used in the sterilization process is a very stressful treatment for plastic raw materials, which must be treated with care.
The flexible DPTE-BetaBag® has long been considered as the optimal solution for safe, fast, and contamination-free transfer of components (caps, stoppers, or plungers) for aseptic filling lines. However, bad practices can compromise the success of the process.
Non-compliance can result in the presence of microorganisms that could jeopardize production. When terminal sterilization isn’t a possibility (product sensitive to the sterilization process), sterility must be ensured at each step of the aseptic filling process. The best way to ensure this sterility is by preventing all forms of microbial ingress.
Sterilization in DPTE-BetaBag® and containers
There are special considerations when sterilizing rubber stoppers or porous loads inside a DPTE-BetaBag® to ensure an efficient process result. “We are looking for efficiency both in terms of sterilization result and remaining moisture content within the bag,” says Joakim Larsson, Getinge Product Line Manager, Sterilizers.
Sterile assurance/air removal/steam penetration
For proper sterilization, air removal and steam penetration are essential. The Tyvek side of the bag will act as a filter and create a pressure lag between the inside and outside of the bag. To ensure proper air removal before sterilization, it is best to slow down the vacuum rate. Creating a controlled ramped vacuum where the rate is an adjustable parameter allows for optimization of each load.
The second method is to introduce a pre-vacuum hold time. This allows the pressure at the lower vacuum level to equalize before steam is introduced to increase the pressure again. This minimizes the risk that the pressure difference will cause inflation that damages the bag.
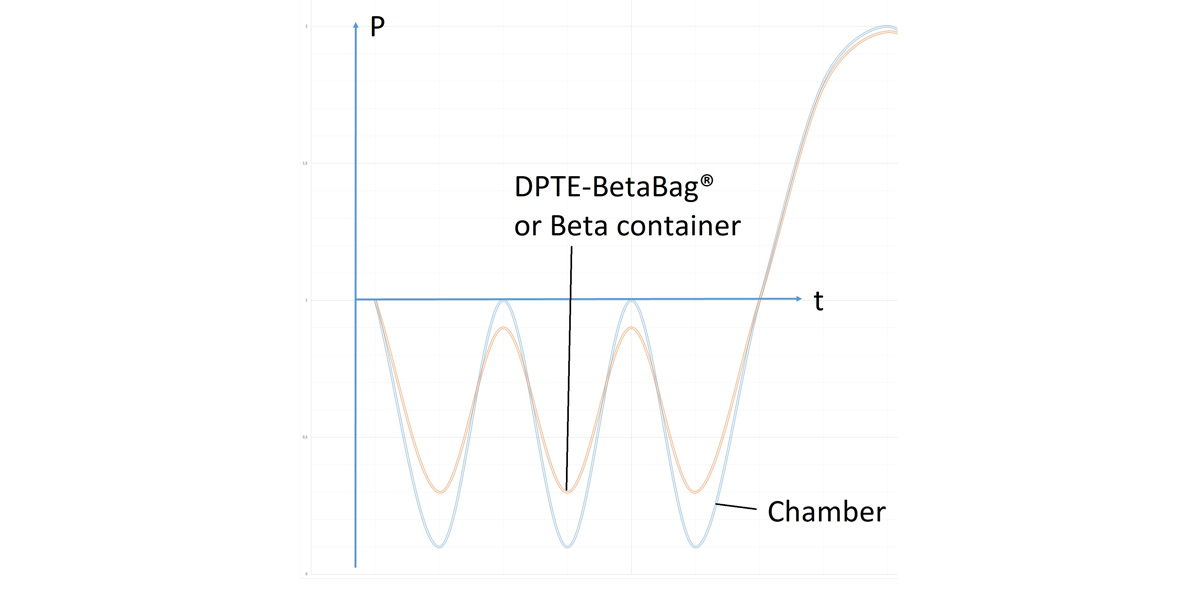
Load dryness
When heating with steam, condensation occurs as the temperature increases. The amount of condensate is proportional to the temperature increase and load weight.
If the load weight is constant, the condensation can be reduced by using dry pre-heat. The load can be heated before steam is directly injected to the chamber and before the air removal phase.
Loads should be heated to approximately 100°C from room temperature to sterilization plateau (20° - 121°C). Pre-heating to 70°C prior to direct steam injection will reduce the amount of condensate by half.
It is also possible to introduce repeated drying pulses after the sterilization plateau using a combination of vacuum and overpressure pulses. Vacuum pulls the moist air out of the bag, while overpressure ensures that dry air is entering through the Tyvek side of the bag and reaching the stoppers.
Each overpressure pulse transfers moisture from the load to the air since there is a drive to equalize to the same moisture level.
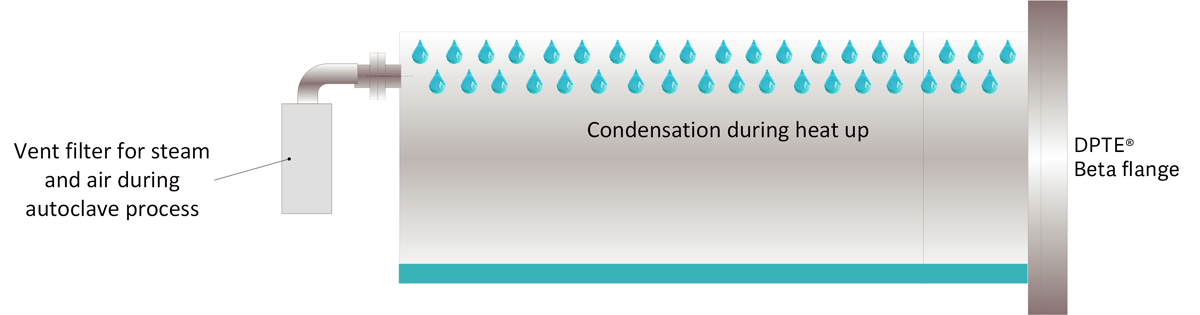
Reducing the ’human factor’ risk
“Years of experience showed us that the human factor is often the root cause of sterility non-compliance,” said Cyril Mounier, Getinge Pharmaceutical Applications Specialist. “Our tendency to overload things can have a significant negative impact on the success of the sterilization process.”
Getinge sought to reduce customers’ overall costs by identifying high-risk practices that could ultimately lead to non-compliance in the autoclaving process. “In 2019, we conducted a series of tests at the Getinge La Calhène facility in Vendôme, France,” Anne-Claude Gilbert, Getinge R&D Plastics Engineer explained.
As the market leader in aseptic transfer solutions, and the originator of DPTE® technology, Getinge set out to identify the parameters that could potentially affect performance of their DPTE-BetaBag® Tyvek bags[1],[2]. These bags are used to autoclave components and load them directly into an aseptic filling line.
“We looked at overall process parameters, as well as elements specific to the sterilization and drying phases,” Anne-Claude said.
It became clear that in order to obtain the best result in terms of seal resistance and bag integrity, DPTE-BetaBag® Tyvek bags should be filled to a pre-determined loading level and undergo a specified autoclave cycle protocol.
What is DPTE®?
DPTE is a French acronym for Double Porte pour Transfert Etanche (double door for leak-tight transfer). It involves interlocking “alpha” and “beta” units, with the alpha part mounted on the containment wall, and the beta part attached to a container or bag. The technology was developed by Getinge La Calhène more than 50 years ago, and is still the gold standard for aseptic transfer.
The DPTE-BetaBag® Tyvek is a combination of a DPTE® Beta part and a bag designed with two films welded together; one side is Tyvek material, and the other is high-density polyethylene (HDPE). The bags hold components – such as caps, stoppers, or plungers – for sterilization in an autoclave and contamination-free transfer into an aseptic zone.
The cost of non-compliance
“We know that bad practices in autoclaving can have significant costs: both the impact of microbial ingress that can cause production failure and the operational costs associated with having to dispose of the affected components and sterilize new ones,” Cyril said.
By identifying the highest-risk elements of the process and setting forth best practices for success, Getinge sought to improve outcomes and reduce customer costs associated with re-sterilization or contamination.
Identifying the most important process parameters
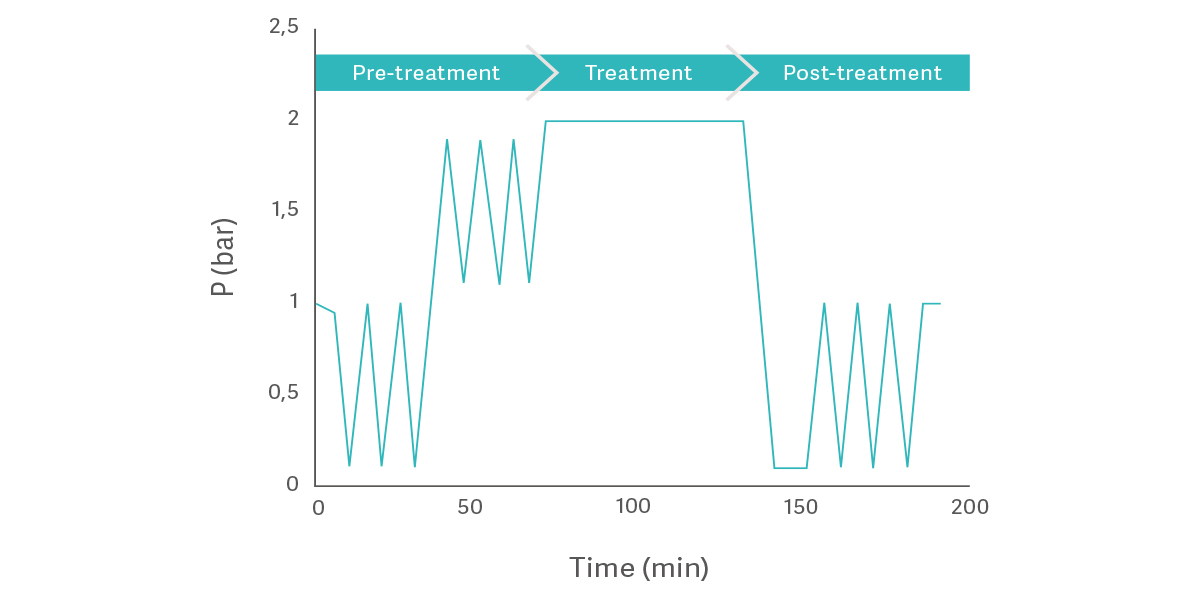
Two comprehensive test programs were conducted by Getinge to analyze specific parameters in the autoclaving process 1,2. These tests analyzed six parameters in three primary categories: general process parameters, sterilization parameters, and drying parameters.
General process parameters looked at basic elements of the process, and how those parameters contributed to the overall success of the process.
- How full are the bags?
- How are they positioned?
Sterilization parameters included time and temperature.
- Does more sterilization time compromise bag integrity?
- Do high temperatures degrade the bag’s performance?
The drying phase presented its own challenges.
- Did the vacuum ramp — the bag inflation and deflation speed during the process cycle — affect bag performance?
- How did pulses affect bag integrity?
A dimensional analysis evaluated how the bag was affected by changes in the six parameters. After each cycle, each bag was measured and tested for bag integrity; because not all bags had visual damage, detailed testing was performed using a Methylene Blue test[3]. Methylene blue is a common test used to identify the presence of channel defects by the leakage of dye through them (ASTM F1929 standard Test Method for Detecting Seal Leaks in Porous Medical Packaging by Dye Penetration) which could permit microbial contaminant to enter.
During each autoclave cycle
The bag inflates and deflates several times according to the pressure modifications inside the sterilizer. Indeed the pressure equilibrium between the autoclave and the DPTE-BetaBag® is not immediate. During the pressure variation in the chamber, pressure differential is created between the autoclave and the bag. Each pressure decrease inflates the bag; each pressure increase deflates it.
“The tests revealed that increased bag deformation correlated with an increased risk of non-compliance,” Anne-Claude said.
The research concluded that sterilization cycle time and the number of post-treatment pulses did not affect bag deformation or bag integrity. However, changes in capacity, position, temperature, and vacuum ramp did have a measurable impact on results. Upon further analysis of these four parameters, best practices were developed.
Best practices for autoclaving success
Optimal results can be achieved by controlling for the four factors of capacity, position, temperature, and vacuum ramp.
Capacity: Avoid overloading
“Much like an overpacked suitcase, overloading a DPTE-BetaBag® Tyvek can affect structural integrity and cause bag damage,” Cyril explained.
Getinge recommends carefully managing the bag capacity to prevent overloading. Maximum filling parameters are as follows:
- 8L load for the 10L DPTE-BetaBag® Tyvek double bag
- 13L load for the 23L DPTE-BetaBag® Tyvek single bag
- 18L load for the 25L DPTE-BetaBag® Tyvek double bag
Position: Flat is better, and shelves can be close together
As you can see from Image 4 (available in the white paper), these bags have two distinctly different sides. The Tyvek side is flat, while the DPTE® Beta part is on the HDPE (high-density polyethylene) side. The research showed that users should always lay the bag on its flat Tyvek side to minimize strain on the material. When placed DPTE® side down with the objective to facilitate the bag “breathing” through the Tyvek layer, the bag cannot lay flat; this puts additional and unnecessary strain on the material and increases the risk of non-compliance. The research also showed that it is not necessary to have the Tyvek side on top to facilitate air exchange.
The constraint provided by the shelf above when the bag is inflated during vacuum phase does not adversely affect bag integrity. Users can reduce the distance between shelves to 15 cm to accommodate a greater number of bags and maximize throughput.
Temperature: Ideal range of 121°C to 123°C
Dimensional analysis revealed that temperatures of 125°C and above adversely affect the structural integrity and functionality of the bag. However, temperatures of 121°C, 122°C 123°C, and 124°C were hot enough to provide effective sterilization (to be linked with the exposure time), but not so hot as to cause bag degradation.
Setting the temperature within this 3°C window produced the expected results while minimizing risk to the bag integrity and thus components contamination.
Vacuum ramp: Minimize bag deformity
The vacuum phase in an autoclave has multiple functions: to forcibly remove air to ensure that the steam reaches every corner of every component during pre-treatment step, and to remove steam and dry the components during the drying phase. The bag repeatedly inflates and deflates throughout an autoclave cycle according to the pressure variation of the chamber.
Dimensional analysis of the bag demonstrated that the higher the vacuum ramp, the greater the elongation of the bag; the positive and negative pressures cause a greater variation in bag shape.
The greater the elongation, the higher the risk of bag degradation from film breakage. As the structural risk increases beyond 0.5 bar/min, it is recommended to maintain pressures below this level.
Following best practices delivers the best results
You can reduce the risk of DPTE-BetaBag® Tyvek degradation by following the best practices for load and autoclave parameters. This can save your facility money that would otherwise be wasted by non-compliant cycles.
- Do not overload the bag beyond the parameters noted by the manufacturer
- Place bag flat, on the Tyvek side
- Maintain maximum temperatures between 121°C and 123°C
- Set the minimum acceptable value for the vacuum ramp to prevent bag deformation
Following these four simple steps can help your organization ensure sterilization success and maintain sterility until the transfer.
Download the white paper here:
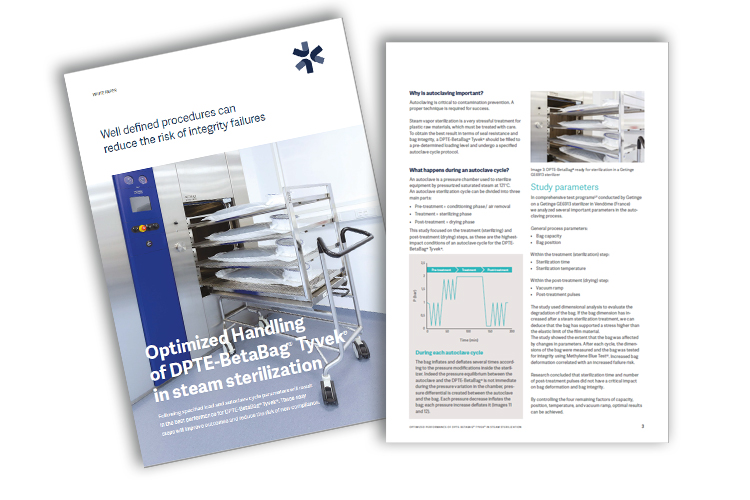
Following specified load and autoclave cycle parameters will result in the best performance for DPTE-BetaBag® Tyvek®. These easy steps will improve outcomes and reduce the risk of bag failure.
Understand how the performance of the DPTE-BetaBag® Tyvek will be optimized by using proper procedures.