Box-to-Bench solution for lab-scale cultivation
- No more preparing bioreactors
- Eliminate the risk of cross-contamination
- Perform more experiments in a shorter time with less work
- Improve reproducibility and outcomes of your experiments
Easily scale-up your bioprocess with single-use bioreactors in 500 mL, 3 L and 15 L.
Easily configure your bioreactor to match your application
The AppliFlex ST is different from other single-use bioreactors. It is a fully customisable stirred tank bioreactor. We use 3D printing technology to create any head plate configuration that is optimal for your bioprocess.
These single-use bioreactors are modeled directly on our world standard autoclavable bioreactors and you can be assured each bioreactor meets similar high standards and quality that you enjoy with our glass bioreactors.
This Applikon bioreactor straight to your lab
Are you interested in the single-use Applikon bioreactor, and would you like to get a virtual sample right now? Try these bioreactors in Augmented Reality*.
Scan the QR code on your desktop with your mobile device or click on the link directly on the mobile device and discover how the AppliFlex would be on your bench.
*View this page on an Augmented Reality (AR) compatible device. Augmented Reality (AR) adds digital elements to the camera of your smartphone, creating the illusion that holographic content is a part of a physical world around you.
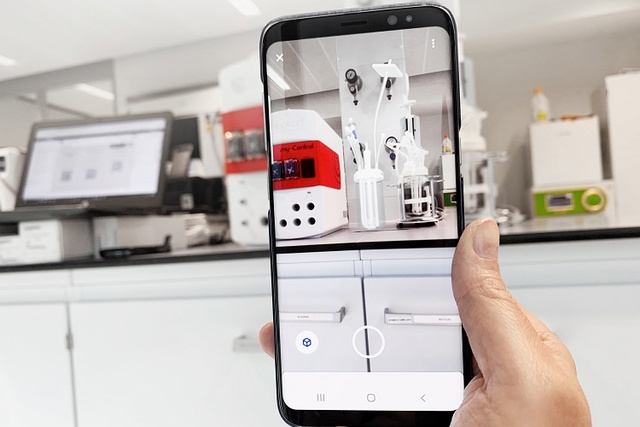
Applikon AppliFlex ST 500 mL
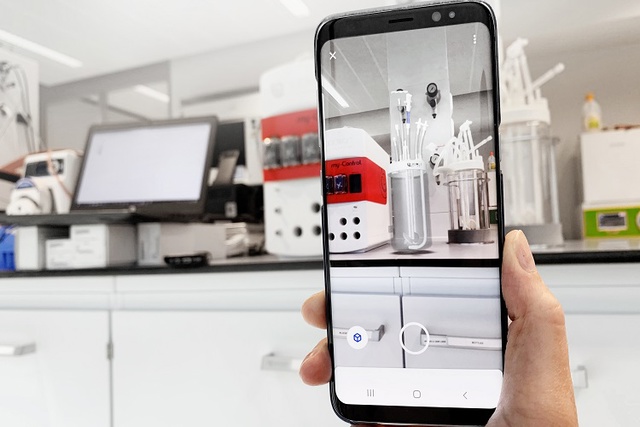
Applikon AppliFlex ST 3 L
Scale up to larger single-use bioreactors for higher productivity.
Explore the Applikon AppliFlex ST 3 L in your lab.
![]() |
From Box-to-Bench
Your bioreactor is ready for operation straight from the box. Take your pre-assembled bioreactor from the box, and get started right away. No laminar flowhood, water supply or drain needed, enabling a smooth and fast workflow.
Save time and costs, execute more runs, and reduce your time-to-market.
Full customisable design
Using 3D printing technology allows for easy optimisation of the bioreactor to match your process and application. The headplate can be configured to your unique needs from special ports, sampling lines, connectors, and spargers to addition bottles.
Bring your design to life with a custom AppliFlex ST.
No cross-contamination
The pre-sterilized bioreactor makes your life in the lab easy. No more assembling and sterilizing before you can start your culture. No more cleaning after the culture is finished. Minimal operator handling reduces the ever-present risk of contamination.
Using single-use sensors allows for a fully closed operation, ensuring sterility in your bioprocess.
Specifications
Physical characteristics | 500 mL | 3 L |
15 L | ||
Dimensions ( h x Ø ) | 236 mm x 75 mm | 340 mm x 130 mm | 500 mm x 223 mm | ||
Weight | 0.2 kg (1 bioreactor) | 0.7 kg (1 bioreactor) | 1.7 kg (1 bioreactor) | ||
Bottom | Dished bottom | ||||
Total volume | 575 ml | 3 L | 15 L | ||
Working volume | 100 – 400 ml | 0.65 – 2.4L | 3 - 12 L | ||
H/D ratio total volume | 2.0 | ||||
H/D ratio working volume | 1.33 | ||||
Impeller type | Marine / Rushton / Anchor / None / Hydrofoil / Helical and more... | ||||
Impeller diameter | 28 mm | 52 mm | 89 mm | ||
Sparger type | Pipe with Ø2mm hole / Open pipe / Sparger stone / Jet sparger / Porous sparger and more... | Porous sparger | |||
Operating conditions | |||||
Working temperature | 5 – 45 °C | ||||
Storage temperature | -80 – 45 °C | ||||
Design pressure | 0 – 0.5 barg | 0 – 0.1 barg | |||
Mixing time | ~3 seconds | ||||
Sterilization | >25 kGy Gamma irradiation | ||||
Sensors options | Single-use sensors or traditional multi-use sensors |
Applications
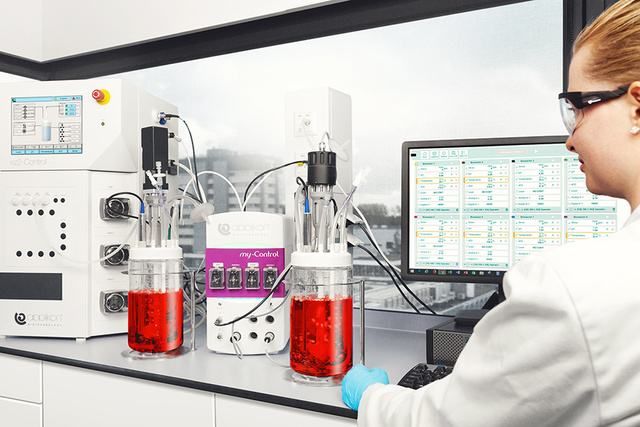
The AppliFlex ST is ideal for the following applications:
- Cell line development, process development and scale up studies
- Batch, fed-batch and perfusion
- Cell and Gene applications (IPC’s, T&NK Cells, and MSc’s)
- Cell culture applications (CHO, HEK, BHK and Sf9)
- Fermentations (S. cerevisiae, K. lactis, B. subtilis and E. coli)
Customised single-use AppliFlex bioreactors with various impellers and ports to match bioprocessing needs
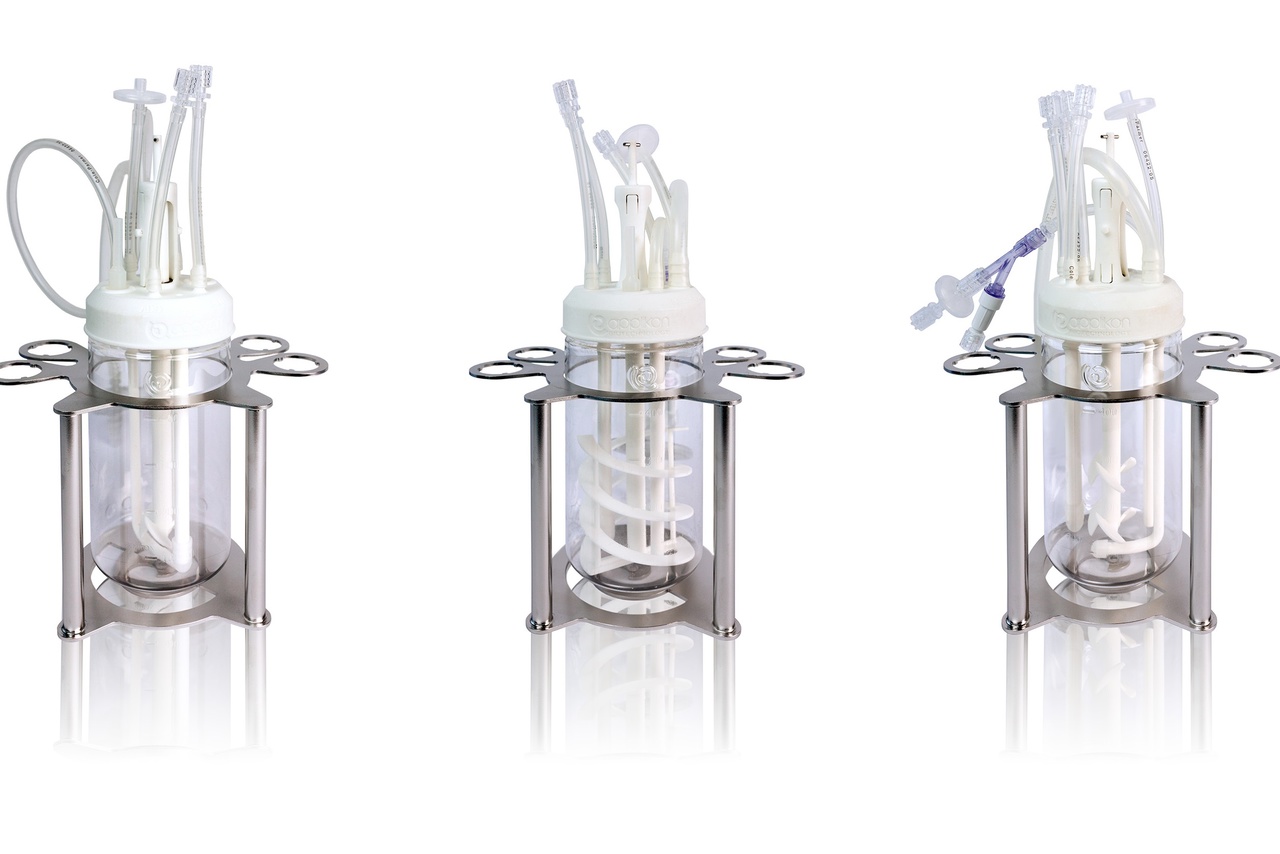
Articles
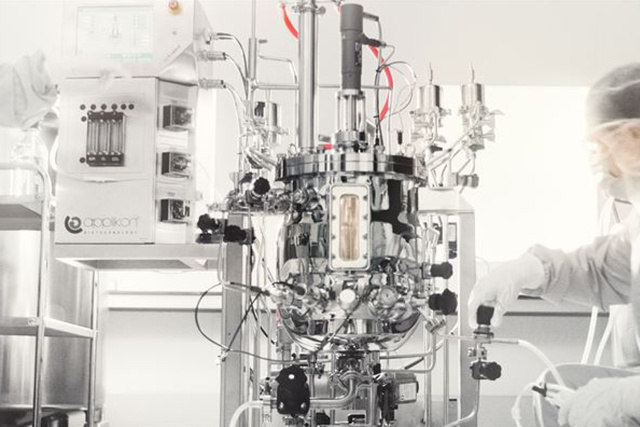
Getinge’s bioreactors to support unique Dutch cellular agriculture initiative
The Dutch government confirms the allocation of €60 million to support an ecosystem around cellular agriculture, the technology used to produce animal products such as meat and milk proteins directly from animal and microbial cells. As a member of the Cellular Agriculture Netherlands Foundation, Getinge will support the project with its bioreactors and bioreactor knowledge.
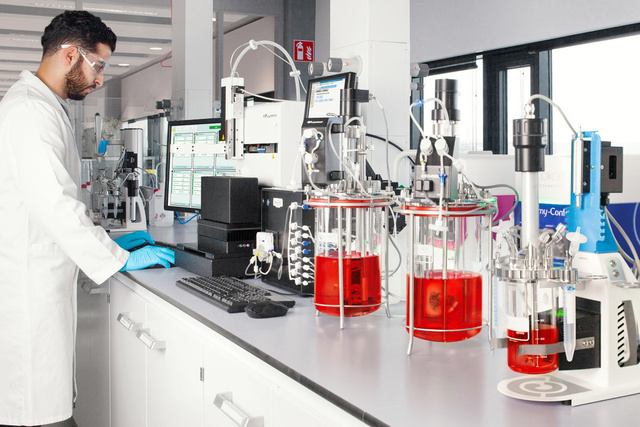
Bioreactors pave the way for eating seafood without fishing
Recently, Bluu Seafood in Germany presented their first market-ready products made from cultivated fish cells – a milestone in enabling people to eat seafood without compromising animal welfare or straining marine ecosystems. Instead, the cells used to make fish fingers and fish balls are growing in bioreactors supplied by Getinge.
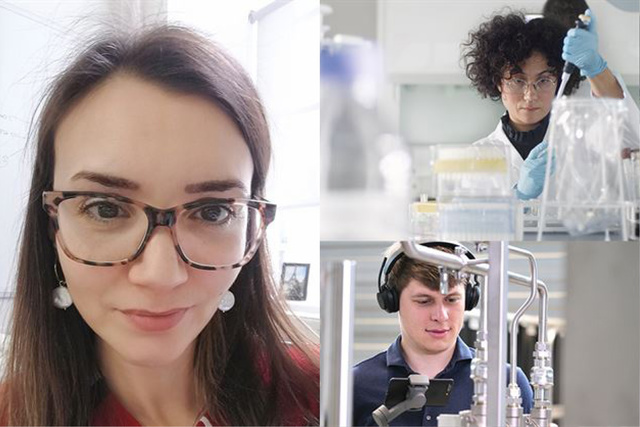
Bioreactors to help grow cellular agriculture
Though the global population is expected to reach 10 billion in 2050, resources to feed everyone are limited. One way to help solve the challenge is the revolution of Cellular Agriculture, an area where Getinge’s bioreactors can play an important role.
On Demand Webinars
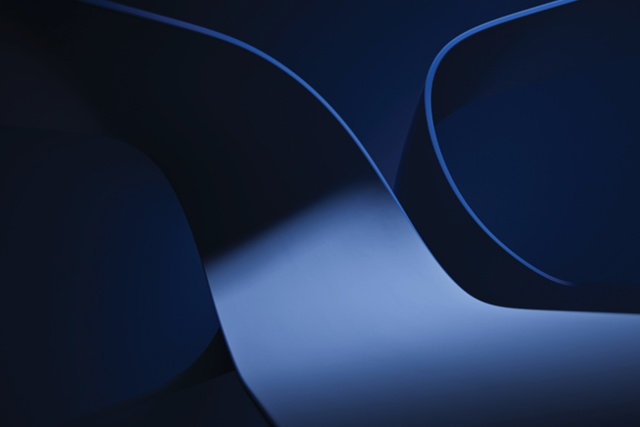
Cellular Agriculture - The Future of Food
by Imko Gaastra - Product Manager, Getinge Life Science & Dr. Mariana Petronela Hanga - Lecturer Biochemical Engineering, UCL
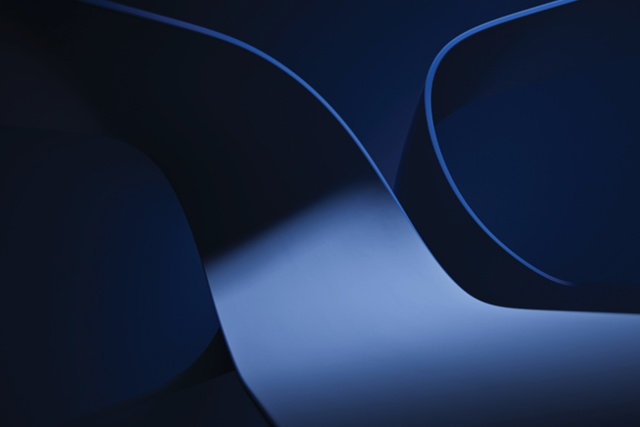
GMP Biomanufacturing Solutions
Walk the Halls of Getinge Applikon following a Stainless Steel Project
Marketing Sales - Sales Flyer
-
Optimised performance and fast bioreactor setup